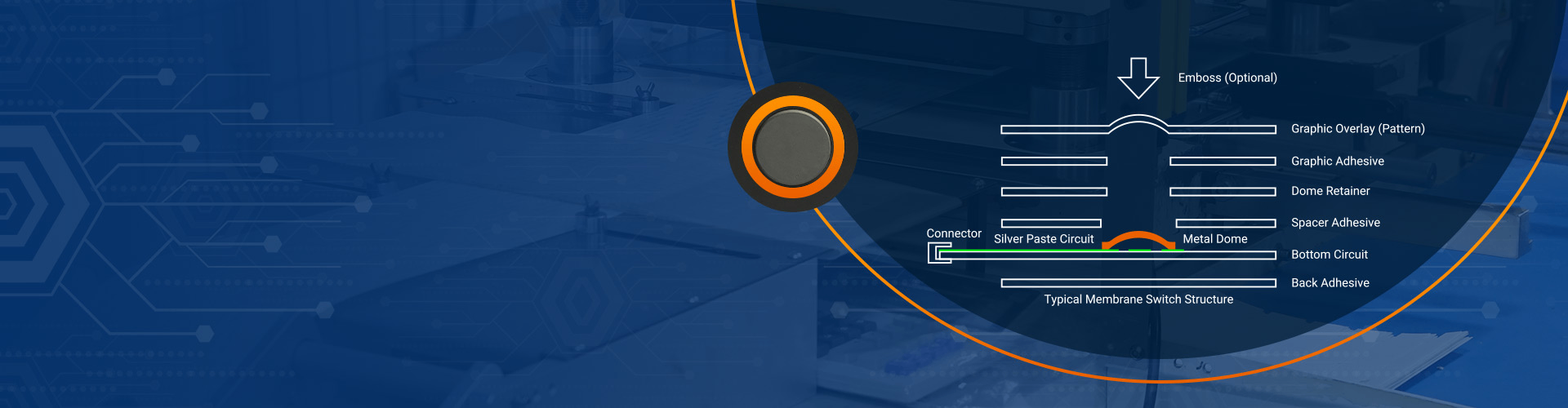
Custom PCB Cost Per Unit: How to Calculate it?
Custom PCB Cost Per Unit: How to Calculate it?
Printed Circuit Boards (PCBs) are crucial components used in a wide range of electronic devices. Whether you’re designing a new product or upgrading an existing one, understanding the cost of a custom PCB per unit is essential for budgeting and production planning. The price of custom PCBs varies widely depending on several factors. In this blog, we will explore how to calculate the cost of custom PCBs, the key factors that influence their prices, and how you can reduce costs while maintaining quality.
What is a PCB in Membrane Switch?
A PCB in a membrane switch is the base layer that supports the electronic connections between various components. In a membrane switch, the PCB is responsible for facilitating the electrical communication between the switch mechanism and the rest of the circuit. This setup is crucial for applications in everything from household appliances to industrial equipment. The PCB in these systems is typically designed to be thin, flexible, and reliable under various conditions, making it a perfect partner for membrane switches.
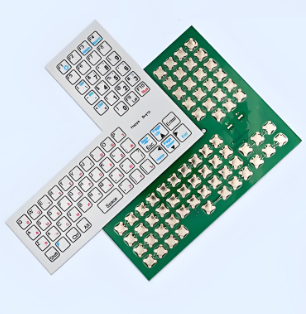
How Much Does a PCB Cost Per Unit?
The cost of a custom PCB per unit can vary significantly based on several factors, such as the complexity of the design, the materials used, and the quantity being produced. In general, smaller production runs tend to be more expensive per unit because the setup costs are spread over fewer boards. As production volumes increase, the per-unit cost tends to decrease. However, it’s not just about volume—design and material choices also have a major impact on pricing.
For example, a simple, single-layer PCB can cost as little as $1 to $10 per unit. More complex multi-layer boards can cost anywhere from $5 to $50 or more per unit, depending on their specifications. Special materials or features, such as gold plating or flex circuits, can also add to the cost.
How to Calculate PCB Design Cost?
Calculating the design cost of a PCB involves several stages:
1. Design Complexity: The more complex the design, the higher the cost. More layers, intricate routing, and tighter tolerances all increase design time and cost.
2. Materials: The type of material you choose, such as FR4, Rogers, or ceramic, will affect the price. Specialty materials tend to be more expensive than standard ones.
3. Labor and Design Time: The more time it takes to design the PCB, the higher the labor cost. If you require specific functionality or certifications (like UL or RoHS compliance), the design process will take longer and cost more.
4. Testing and Prototyping: Before going into full production, PCBs usually undergo testing and prototyping, which adds to the cost.
A rough way to calculate the PCB design cost is to account for the hourly rates of designers and the number of hours required to complete the design. This, combined with material and prototyping costs, gives you a reasonable estimate.
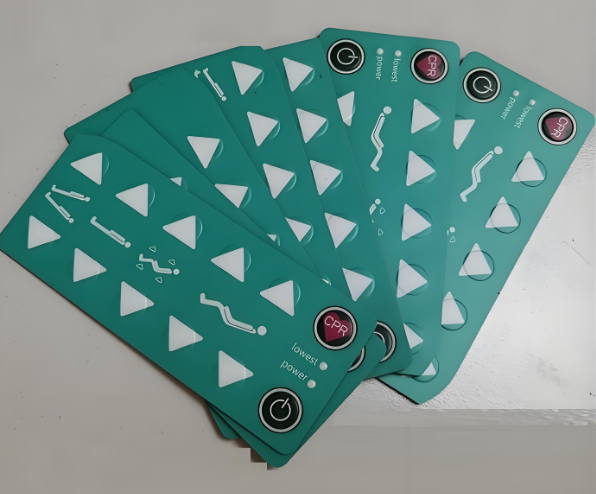
Why Are Custom PCBs So Expensive?
Custom PCBs often come with higher costs for several reasons:
1. Unique Designs: Custom PCBs are made to fit the specific needs of a project. The more unique the design, the higher the cost, as custom work typically requires more time and expertise.
2. Material Selection: Custom boards might use specialized materials that are more expensive than standard PCB materials like FR4. For example, materials like aluminum or ceramic can increase costs but offer better performance in high-temperature or high-power applications.
3. Low Volume Production: When only a small number of units are required, manufacturers can’t spread out the costs of setup and design across a large batch, making each unit more expensive.
4. Prototyping and Testing: Custom boards usually need to be tested more rigorously, especially for complex designs. This process adds both time and cost.
Key Factors That Affect the Cost of PCB
Several factors influence the final cost of a custom PCB. These include:
- Board Size and Complexity: Larger boards or those with more layers and components naturally cost more due to increased production complexity. A smaller, single-layer board will cost less than a large, multi-layer one.
- Materials: High-performance materials can significantly increase the price of a PCB. For example, boards designed for high-frequency applications may require special substrates, adding to the cost.
- Volume: The number of units ordered has a direct impact on the price per unit. While the per-unit price can be high for small production runs, larger orders benefit from economies of scale.
- Lead Time: A shorter lead time can result in higher prices due to the need for expedited production or shipping.
- Finishing Options: Special finishes, like gold plating or surface treatments, will increase the cost. These finishes improve the durability and performance of the board but come at a price.
- Testing and Certification: More advanced or specific testing requirements will increase costs. Certifications like UL or RoHS can also add to the final price.
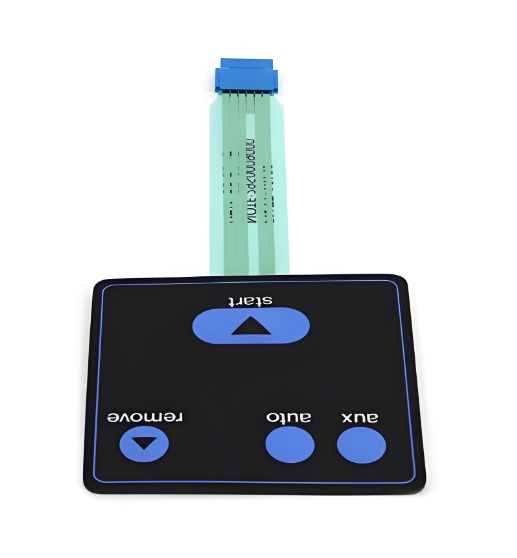
Tips to Reduce Custom PCB Cost Per Unit
Reducing the cost of custom PCBs without sacrificing quality is possible with a few strategic steps:
- Increase Volume: Ordering larger quantities can significantly lower the cost per unit, as manufacturers can spread their setup costs over a greater number of units.
- Simplify the Design: Simplifying the PCB design can lower costs. Reducing the number of layers or components can cut down on both material and manufacturing costs.
- Choose Standard Materials: Using standard materials like FR4 rather than specialized ones can help reduce costs without compromising performance.
- Optimize for Manufacturing: Designing your PCB with manufacturing in mind can help reduce costs. Avoid overly tight tolerances, complex routing, and unnecessary components that may be expensive to produce.
- Plan Ahead: Avoid rushing the process. Short lead times often result in higher costs. Planning production schedules in advance gives manufacturers more flexibility and can reduce prices.
- Prototype Efficiently: Rather than jumping straight into production, use prototyping to catch any design flaws early. This can save money on revisions and prevent costly mistakes in the final production run.
- Work with Experienced Suppliers: Partnering with a reliable PCB manufacturer who understands your needs and can offer cost-saving advice can make a big difference in overall costs. Look for a supplier with a strong track record of delivering quality and cost-effective PCBs.
Conclusion
The custom PCB cost per unit is influenced by a range of factors, from design complexity to materials, volume, and lead time. By understanding these factors and following some of the tips for reducing costs, you can create a PCB that meets your requirements without breaking the bank. Whether you’re working on a small-scale project or large-volume production, it’s important to balance cost with quality to ensure a successful outcome.
By working closely with experienced PCB manufacturers and optimizing your designs, you can minimize costs while maintaining the high standards required for your projects. If you’re ready to get started on your custom PCB design or need expert advice on cost-saving strategies for your membrane switch projects, Yuan Electronics is here to help. Our team offers top-quality PCBs with a focus on affordability and reliability. Reach out to us at sales@best-membraneswitch.com for more information!
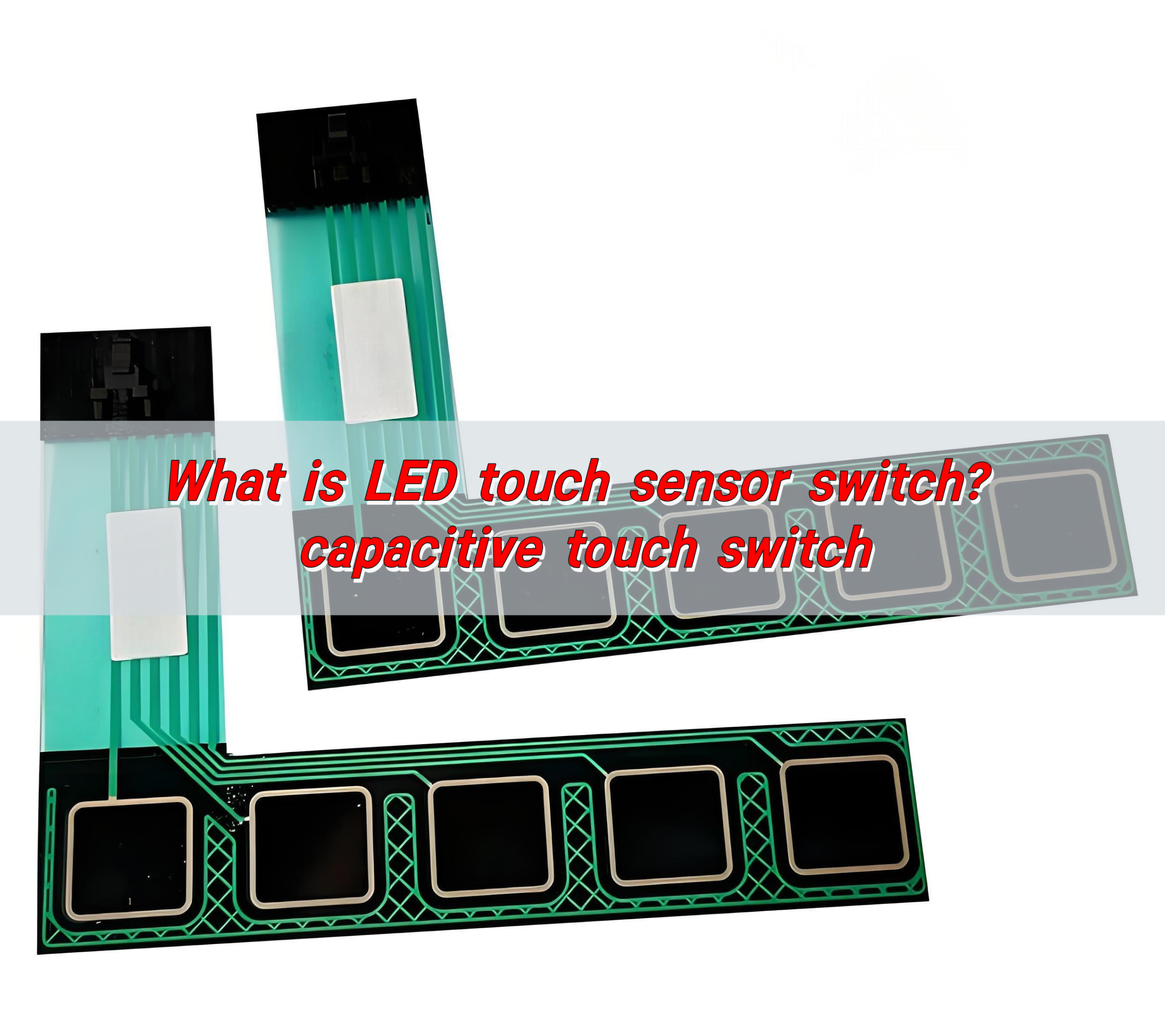
What is LED touch sensor switch? capacitive touch switch
The LED touch sensor switch is an electronic component that combines an LED light and a touch sensor. It controls the on and off of the LED light by touching it, achieving energy-saving and convenient lighting control. It uses capacitive sensing technology to detect human proximity or touch, thereby controlling the on and off of ...
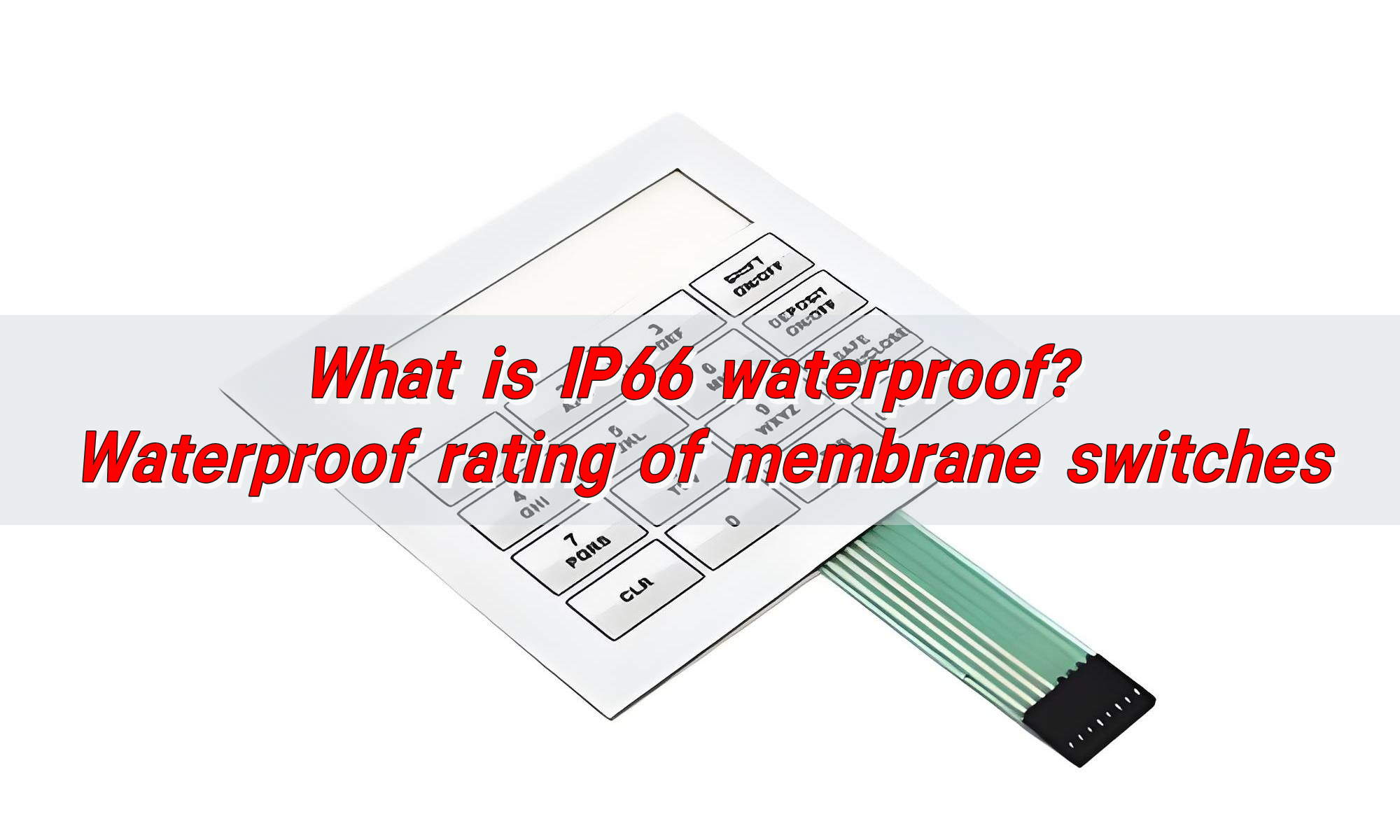
What is IP66 Waterproof? Waterproof Rating of Membrane Switches
The IP66 waterproof rating means that the device is completely protected from dust ingress and can withstand strong water jets. The waterproof rating of membrane switches can usually reach IP67, which is achieved through special processes and materials to ensure its reliability in humid or rainy environments. This performance makes membrane switches suitable for scenes ...
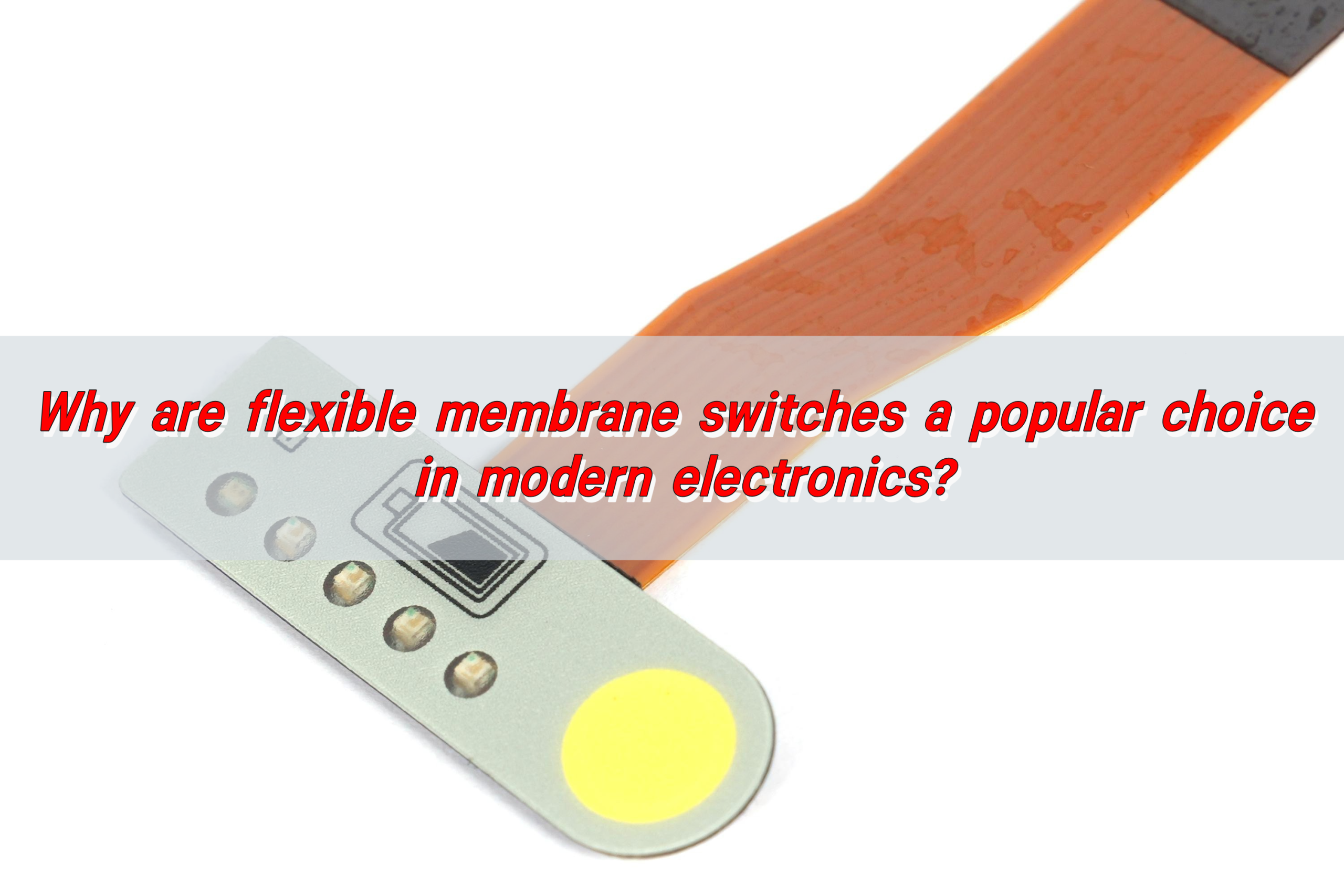
Why are flexible membrane switches a popular choice in modern electronics?
Flexible membrane switches are popular in modern electronic products due to their flexibility, thinness and economy. They not only adapt to complex curved surfaces and achieve flexible design, but also have environmental adaptability such as waterproof and dustproof. In addition, they support multi-function integration, such as LED indicators and sound feedback, to enhance user experience. ...
Contact us online