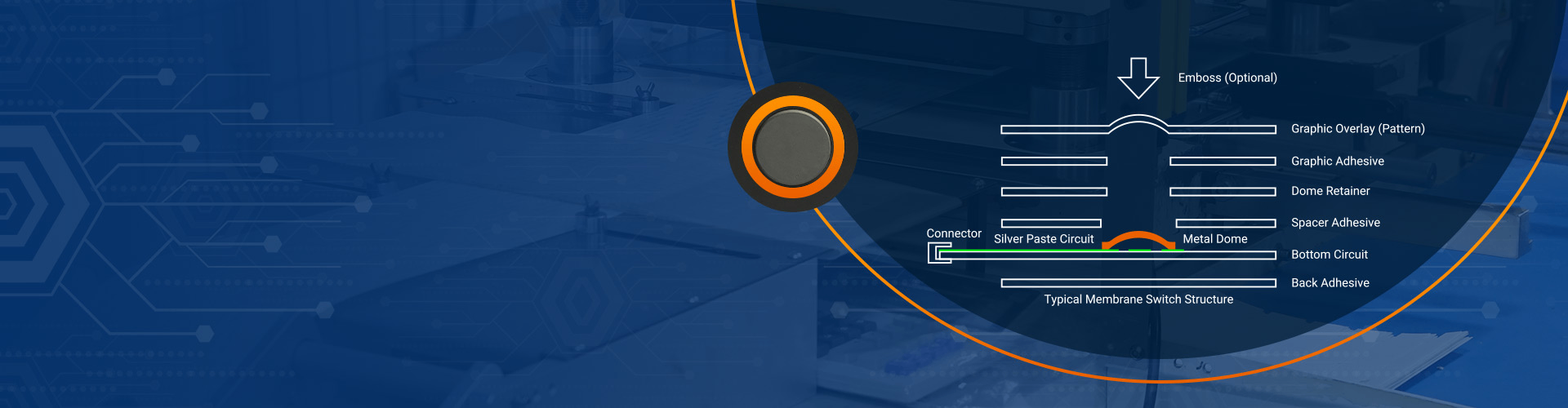
What is Wear Test for Membrane’s Mechincal?
What is Wear Test for Membrane’s Mechincal?
Membrane switches are widely used in various industries due to their reliability and flexibility. However, like any other product, they undergo wear and tear through daily use. This is where the wear test comes in—an essential process to assess the durability and functionality of membrane switches under mechanical stress. This blog will explain what a mechanical wear test is, its purpose, the methods used, how to perform it, its importance for membrane switches, and ways to improve their wear resistance.
What is the Mechanical Wear Test?
A mechanical wear test evaluates how well a membrane switch can withstand repeated mechanical actions, such as pressing or rubbing. The test simulates real-life usage, exposing the membrane to various mechanical stresses over time.
In the case of membrane switches, the mechanical wear test focuses on how the switch holds up against repeated button presses. These tests often involve placing the membrane under specific conditions, like varying pressure or movement, to simulate extensive use. The results help designer or manufacturers understand how long the product can remain functional before its surface degrades or its performance drops.
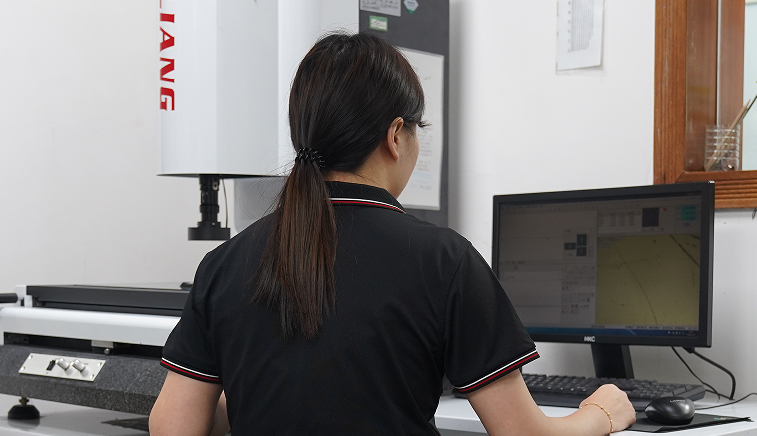
What is the Purpose of the Wear Test?
The purpose of a wear test is to measure the durability of the membrane switch’s surface and internal components under continuous mechanical stress. By subjecting the membrane to simulated use, manufacturers can determine whether the switch will perform reliably over time.
The wear test aims to assess:
- Durability: How well the membrane switch maintains its function after repeated use.
- Reliability: Ensuring that the switch continues to work without failure, even after extensive mechanical interaction.
- Performance consistency: Checking if the switch’s response time or tactile feedback changes over time.
- Material resilience: Evaluating the wear resistance of the materials used in the membrane switch, such as the polyester film or conductive ink.
What Are the Methods of Wear Testing?
There are several methods used to test the mechanical wear resistance of membrane switches. The choice of method depends on the product’s design, usage conditions, and the specific test requirements. Here are some common methods used in wear testing:
1. Button Press Simulation
This method involves using a machine to simulate repeated button presses. The machine presses the switch multiple times at varying speeds, replicating the usage of the switch over a long period. The number of presses is counted until the switch fails or shows signs of degradation.
2. Abrasion Testing
Abrasion testing evaluates how the membrane switch’s surface holds up to friction. This test is crucial for switches exposed to harsh environments, where physical contact with surfaces or objects may cause wear. A specialized machine scrubs or rubs the membrane to mimic continuous contact.
3. Tensile Testing
This method tests the switch’s resistance to forces that could stretch or pull it. A tensile tester applies force to the membrane to check how it responds to mechanical stress, ensuring the material doesn’t tear or lose functionality when stretched.
4. Environmental Stress Testing
While not a wear test per se, environmental testing also plays a role in wear resistance. This method exposes the membrane switch to extreme conditions, such as high temperatures or humidity. Meanwhile, it assesses how these conditions affect the membrane’s ability to perform under mechanical stress.
How to Perform a Wear Test?
Performing a mechanical wear test on a membrane switch involves setting up the switch under controlled conditions that simulate real-world usage. Here’s how to conduct a typical wear test:
Step 1: Prepare the Test Setup
First, set up the membrane switch in a testing environment. This might involve mounting the switch onto a test panel, ensuring that the switch’s surface is clean and free of debris. It’s essential to set the environment to mimic the conditions the switch will face in the field.
Step 2: Select the Test Method
Choose an appropriate test method based on the desired outcome. For example, if you are testing for button press durability, set up a button press simulation machine. If testing for abrasion, place the membrane under the rubbing machine.
Step 3: Run the Test
Begin the test by activating the machine to start the simulation. It’s common to test the switch for thousands or even millions of cycles, depending on the product’s intended lifespan. Record the number of cycles completed before the switch shows any signs of failure, such as a decrease in tactile feedback or functional malfunctions.
Step 4: Monitor Performance
Monitor the membrane switch throughout the test to ensure that no issues arise prematurely. Check for any signs of fading or degradation, such as the fading of printed markings or failure of the switch to register inputs correctly.
Step 5: Analyze Results
Once the test is complete, analyze the results to determine the wear and tear. Evaluate whether the membrane switch still meets the required specifications after the testing phase. If any failure occurs, determine whether the issue is related to the material or the switch’s design.
Why is the Mechanical Wear Test Important for Membrane Switches?
The mechanical wear test is critical for membrane switches because it helps ensure the product’s reliability, safety, and long-term usability. Here’s why it’s so important:
- Due to membrane switches are used in a wide variety of applications, from industrial machines to consumer electronics. A mechanical wear test ensures that the switch will continue to function properly even after years of repeated use.
- Testing can identify potential weaknesses in the design or materials, enabling manufacturers to make improvements before the product reaches the market. This leads to better performance and fewer defects after the switch is in use.
- By identifying wear-related issues before products are shipped, manufacturers can reduce the likelihood of product returns or warranty claims.
- Many industries require that components meet specific performance standards. Mechanical wear testing helps ensure that membrane switches comply with industry regulations, guaranteeing their safety and durability.
- Wear tests provide valuable data on how long a membrane switch is expected to last under normal use.
How to Improve the Wear Resistance of Membrane Switches?
Improving the wear resistance of membrane switches involves choosing the right materials and design approaches. Here are several strategies to increase wear resistance:
1. Use High-Quality Materials
The quality of the materials used in the construction of a membrane switch has a direct impact on its wear resistance. For example, using high-grade polyester or polycarbonate films can enhance the durability of the switch. Similarly, selecting durable conductive inks can ensure that the switch retains its functionality even after extensive use.
2. Optimize Coatings and Laminates
Applying protective coatings or laminates to the membrane switch can significantly improve its wear resistance. These coatings protect the switch from abrasion and other forms of mechanical damage. Consider using coatings with high hardness levels or anti-scratch properties to prevent surface degradation.
3. Design for Durability
The design of the membrane switch itself can also influence its wear resistance. For instance, reducing the number of parts that are directly exposed to mechanical stress can help increase durability. Also, incorporating features such as raised button surfaces or textured layers can help distribute pressure evenly and reduce localized wear.
4. Enhanced Sealing
Ensuring that the membrane switch is adequately sealed can protect it from environmental factors that may contribute to wear. Seals help prevent dust, moisture, and other elements from compromising the switch’s integrity during prolonged use.
At Yuan electronics, we understand the importance of wear resistance in membrane switches. Our high-quality membrane switches are manufactured to withstand the toughest conditions, providing reliable performance and durability for every application. Whether you need a membrane switch for industrial equipment or consumer electronics, do not forget to touch us, we are happy to work with you!
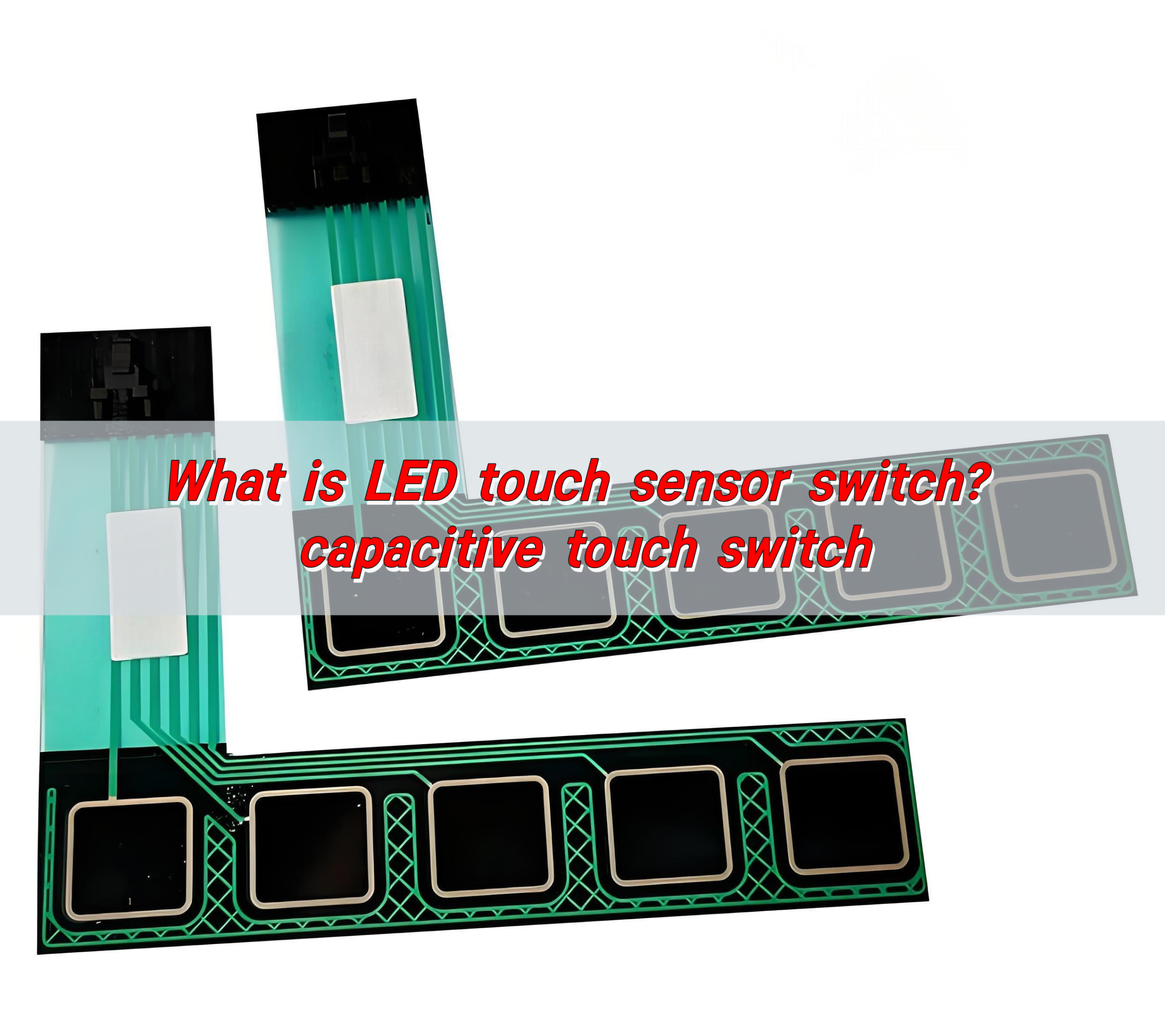
What is LED touch sensor switch? capacitive touch switch
The LED touch sensor switch is an electronic component that combines an LED light and a touch sensor. It controls the on and off of the LED light by touching it, achieving energy-saving and convenient lighting control. It uses capacitive sensing technology to detect human proximity or touch, thereby controlling the on and off of ...
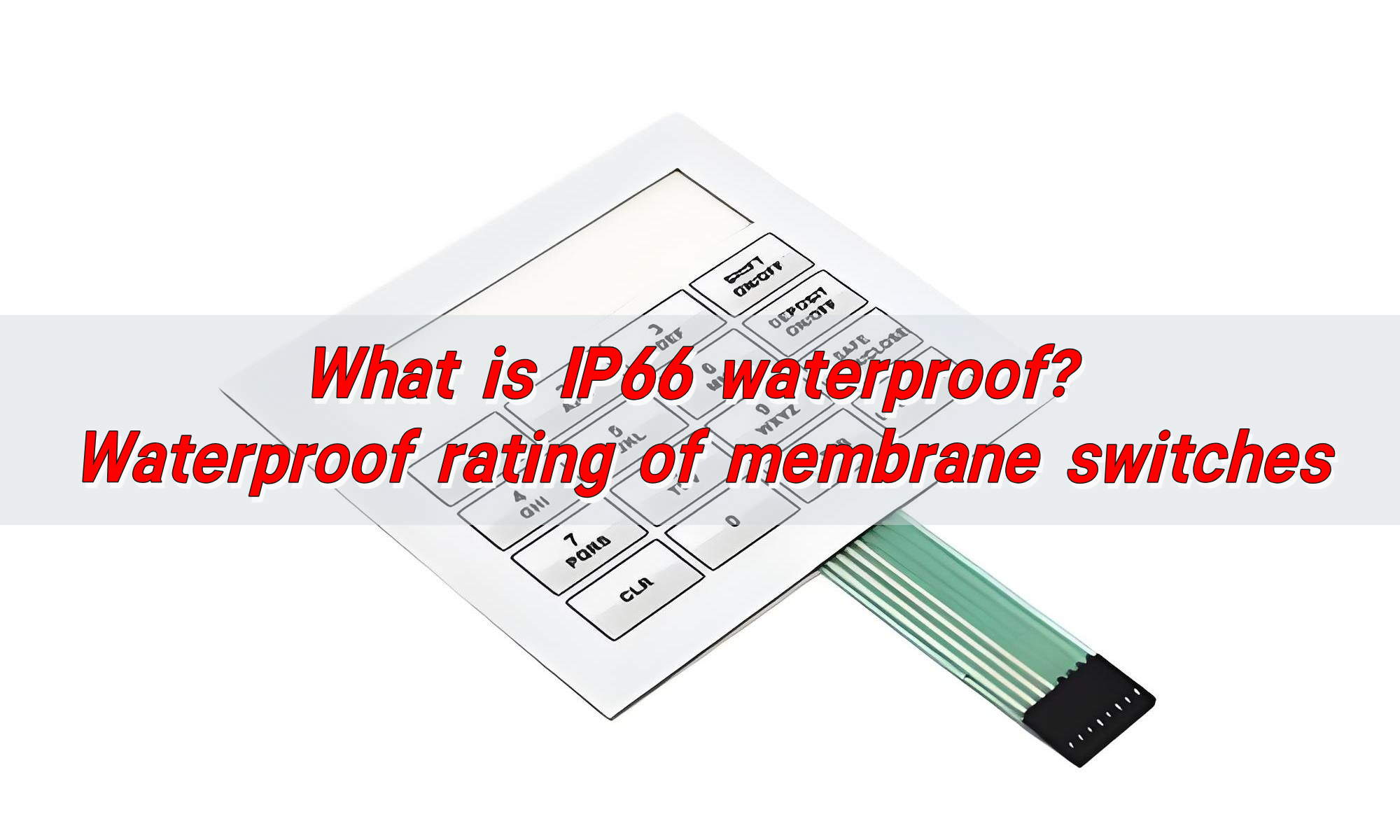
What is IP66 Waterproof? Waterproof Rating of Membrane Switches
The IP66 waterproof rating means that the device is completely protected from dust ingress and can withstand strong water jets. The waterproof rating of membrane switches can usually reach IP67, which is achieved through special processes and materials to ensure its reliability in humid or rainy environments. This performance makes membrane switches suitable for scenes ...
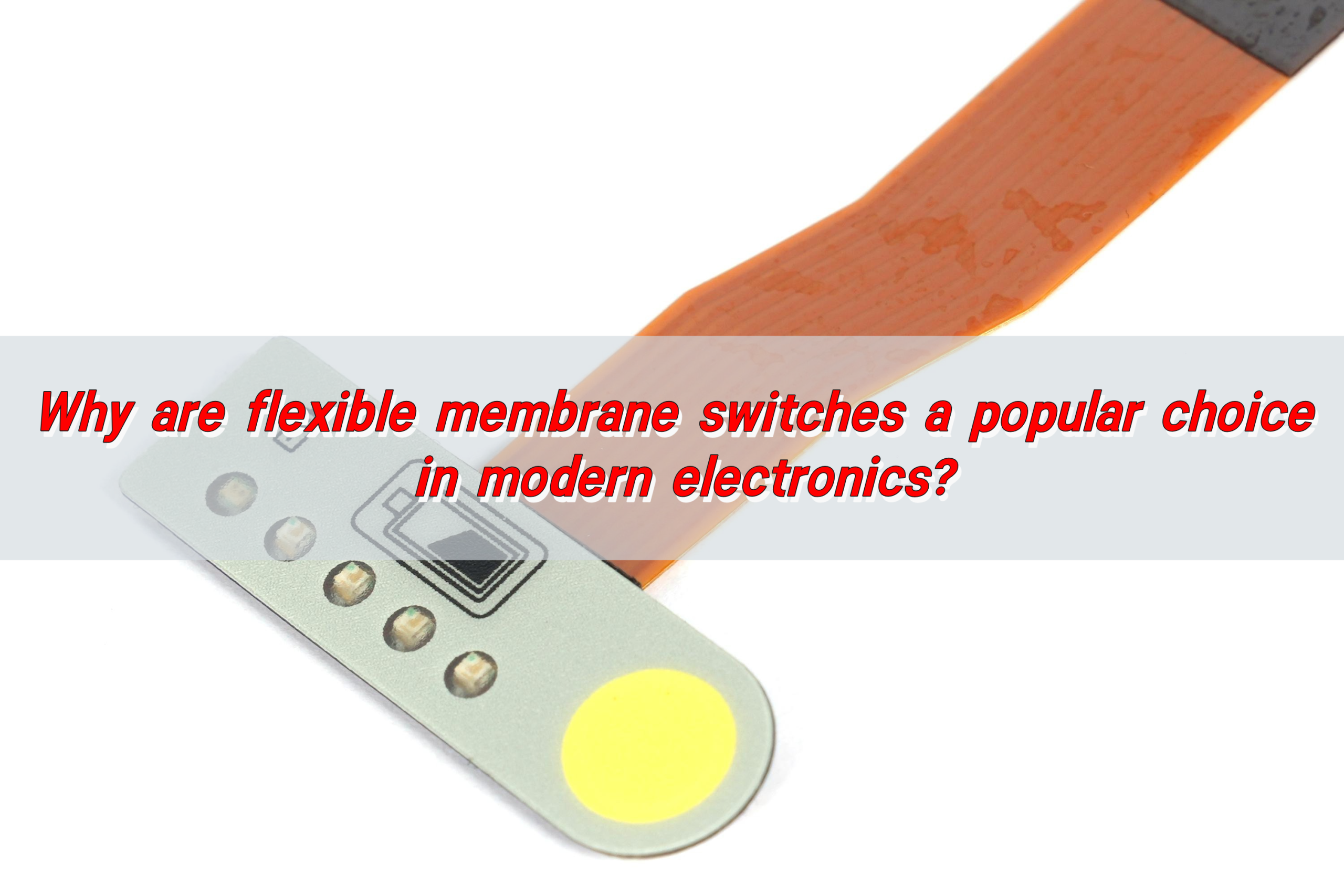
Why are flexible membrane switches a popular choice in modern electronics?
Flexible membrane switches are popular in modern electronic products due to their flexibility, thinness and economy. They not only adapt to complex curved surfaces and achieve flexible design, but also have environmental adaptability such as waterproof and dustproof. In addition, they support multi-function integration, such as LED indicators and sound feedback, to enhance user experience. ...
Contact us online