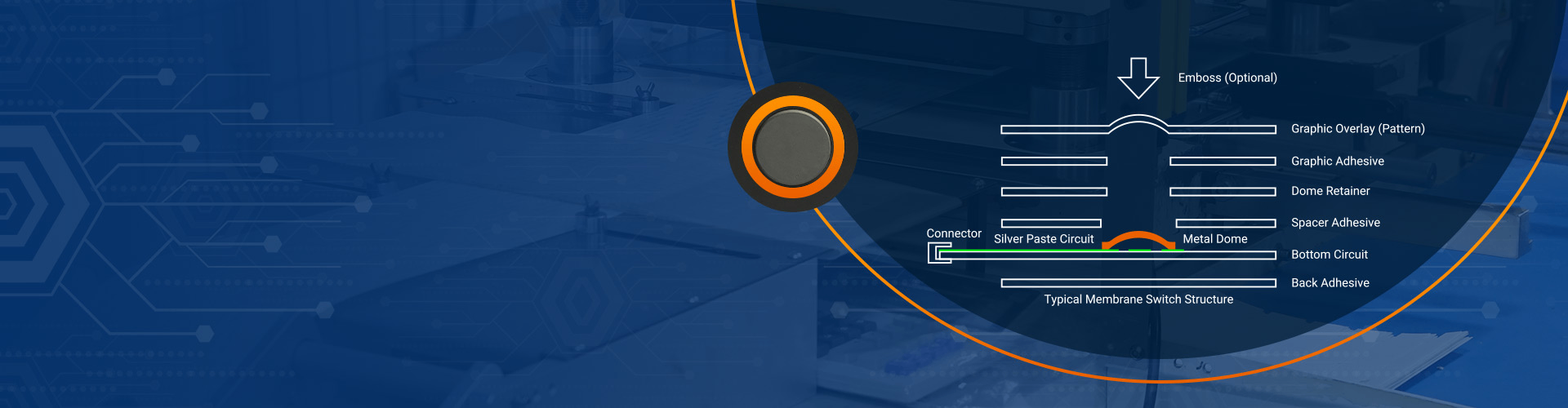
Flexible Rubber MIDI Controller Membrane Panels
Flexible Rubber MIDI Controller Membrane Panels
What Is a Flexible Rubber MIDI Controller?
A flexible rubber MIDI controller is a game-changer for musicians, producers, and performers. Unlike the stiff, traditional controllers, these are soft, lightweight, and, most importantly, flexible. They’re made with special rubber that feels great to touch and offers a unique level of interaction.
These controllers are ideal for all types of users. Whether you’re a professional musician looking for precision or someone just starting out in music production, the flexibility and simplicity make them a must-have tool. Their adaptability fits into any setup, whether you’re performing on stage or tinkering in your home studio.
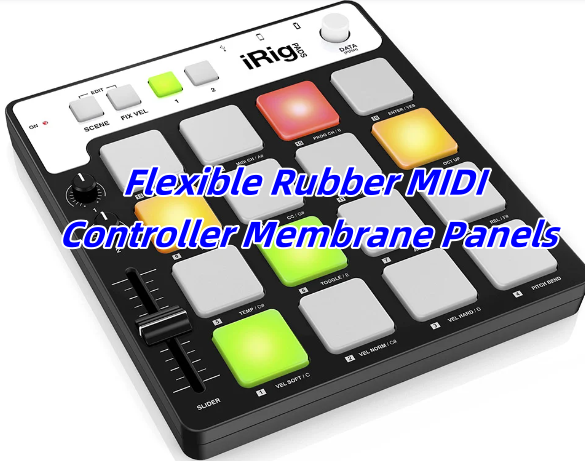
How Does a Flexible Rubber MIDI Controller Work?
The functionality of a flexible rubber MIDI controller lies in its ability to translate physical interaction into digital signals. The surface of the controller is embedded with sensors that detect touch, pressure, and movement. These sensors interpret your actions and generate MIDI signals—the standard communication language used by music devices and software.
When a user interacts with the controller, whether through tapping, sliding, or pressing, the sensors detect the input and transmit it to connected devices. Advanced controllers often support multitouch functionality, allowing multiple inputs simultaneously. This enables complex, dynamic interactions, such as controlling multiple parameters or triggering multiple sounds at once.
Advantages of Flexible Rubber MIDI Controllers
Flexible rubber MIDI controllers have gained significant attention for their numerous advantages:
- Portability: The lightweight and flexible nature of these controllers makes them easy to transport. They can be rolled or folded, saving space and enhancing convenience for mobile musicians.
- Durability: Rubber materials are resistant to wear and tear, ensuring longevity even with frequent use. This robustness makes them a reliable choice for professionals.
- Customizability: Many flexible MIDI controllers can be configured to meet specific needs. Users can define control zones, assign functions, and adapt layouts for personalized workflows.
- Ergonomics: The soft, responsive surface enhances comf
- ort during extended use. Its tactile feedback provides a natural interaction experience, reducing strain.
- Compatibility: These controllers integrate seamlessly with various devices and music software, ensuring broad applicability across platforms.
- Versatility: Whether used in live performances, studio production, or casual practice, flexible rubber MIDI controllers excel in diverse scenarios, adapting to user requirements effortlessly.
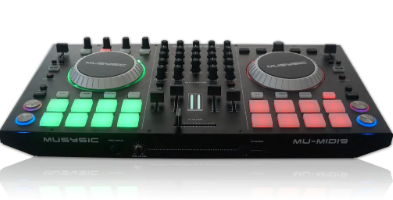
How to Design a Membrane Panel for a Flexible Rubber MIDI Controller?
Designing a membrane panel for a flexible rubber MIDI controller requires a structured approach that considers both functionality and user experience. Each element of the design must align with the specific demands of MIDI control, ensuring precision and responsiveness.
1. Define Functional Requirements
Start by determining the primary functions the membrane panel needs to support. This includes the number of control zones (e.g., buttons, sliders, or pads), their size, and intended interactions such as touch, pressure sensitivity, or gestures. Clear requirements help ensure the design supports the intended use cases, whether for live performances, studio recording, or both.
2. Select Suitable Materials
The choice of rubber material is critical to the panel’s performance. Use high-grade rubber with optimal elasticity, wear resistance, and tactile feedback. It must be robust enough to endure repeated use while remaining sensitive to user inputs. For added durability, consider coatings that resist oil, moisture, or environmental factors.
3. Integrate High-Precision Sensors
The success of the membrane panel lies in its sensor technology. Capacitive or resistive sensors are commonly used, with capacitive sensors offering greater sensitivity and multitouch capabilities. Sensors must be placed accurately beneath the membrane surface to ensure consistent detection of touch and pressure across the panel.
4. Design an Intuitive Layout
The panel layout should prioritize user ergonomics. Group related controls logically, ensuring that buttons, sliders, or pads are positioned within easy reach. Use subtle surface features, such as raised edges or textured areas, to guide users without needing visual confirmation. Incorporating customizable zones can provide users with flexibility in assigning specific functions.
5. Optimize Electrical Connectivity
The membrane panel must integrate seamlessly with the controller’s electronics. Flexible printed circuits (FPCs) or conductive inks are commonly used to connect sensors to the controller’s processing unit. Ensure that traces are designed to minimize signal loss and interference, preserving the accuracy of MIDI output.
6. Enhance User Feedback
To improve usability, consider adding visual or tactile feedback mechanisms. LED backlighting can provide clear visual cues, while haptic feedback (e.g., vibrations) enhances user interaction, especially in low-light environments or live performances.
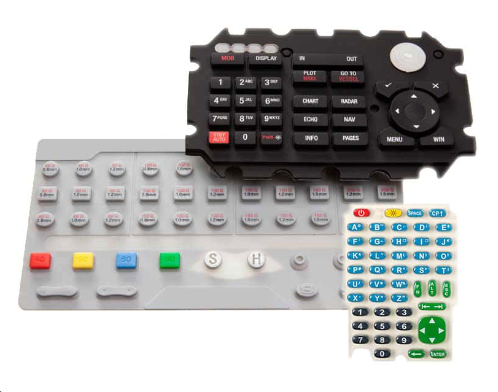
7. Prototyping and Testing
Build prototypes of the membrane panel and conduct rigorous testing. Evaluate the panel’s responsiveness, durability, and user experience. Feedback from musicians and producers can help identify design flaws and areas for improvement. Testing under different conditions, such as varying temperatures and humidity levels, ensures reliability in real-world scenarios.
8. Incorporate Aesthetic and Branding Elements
Beyond functionality, the membrane panel should align with the controller’s overall aesthetic and branding. Use colors, logos, and patterns that enhance visual appeal while maintaining a professional look. Avoid overcrowding the design, as clarity is crucial for usability.
9. Document the Design
Finally, create detailed documentation for the membrane panel design, including specifications, manufacturing processes, and testing procedures.
Manufacturing Process of Flexible Rubber MIDI Controller Membrane Panels
The production of these membrane panels involves precise engineering and quality control. Here is a simply step-by-step overview:
- Material Preparation: High-grade rubber is sourced and prepared for the manufacturing process. The material must meet flexibility and durability standards.
- Sensor Integration: Sensors are embedded into the rubber surface, typically using capacitive or resistive technologies. Accurate placement is critical for optimal performance.
- Shaping the Rubber: Using advanced cutting technologies, the rubber is shaped into the required design. This step ensures alignment with the controller layout.
- Layer Assembly: The rubber surface, sensors, and other components are layered and bonded. This step requires precision to ensure a seamless interface.
- Testing and Quality Assurance: Each panel undergoes rigorous testing to verify its responsiveness, durability, and functionality.
- Final Assembly and Packaging: The completed panels are assembled into the final controller design, cleaned, and packaged for distribution.
FAQs About Flexible Rubber MIDI Controllers
1. What makes flexible rubber MIDI controllers unique?
Their flexibility, portability, and tactile responsiveness set them apart from traditional controllers, offering a more dynamic user experience.
2. Are flexible rubber MIDI controllers suitable for live performances?
Yes, they are highly effective for live performances. Their lightweight design and multitouch capabilities make them ideal for dynamic stage setups.
3. How do I maintain a flexible rubber MIDI controller?
Regular cleaning with a soft, damp cloth is sufficient. Avoid exposing it to extreme heat or chemicals to preserve its quality.
4. Can I customize the functionality of my flexible rubber MIDI controller?
Many models support extensive customization, allowing users to assign functions, modify layouts, and tailor controls to their preferences.
5. Are these controllers compatible with popular music software?
Yes, they integrate seamlessly with most music production software and devices that support MIDI communication.
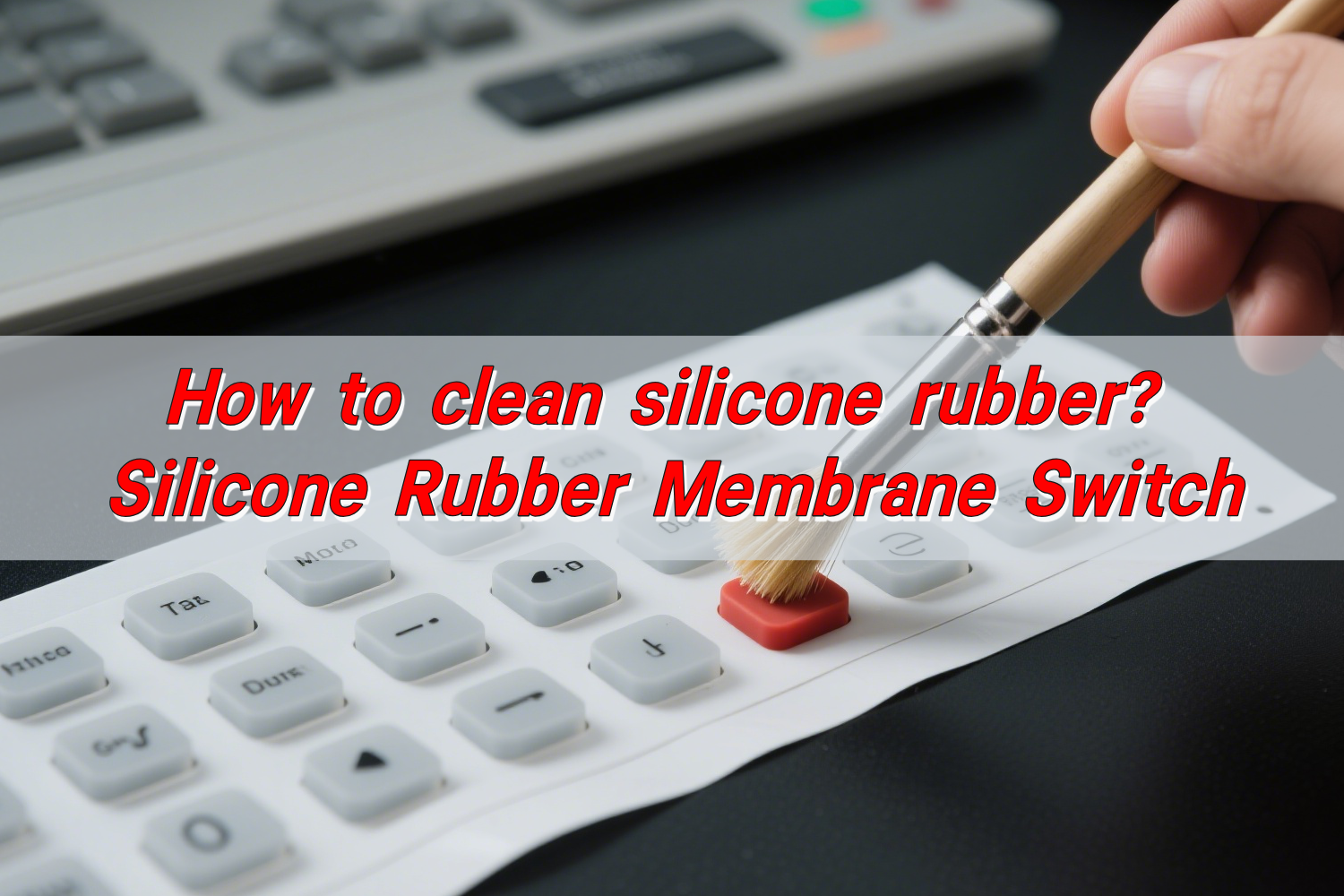
How to clean silicone rubber? Silicone Rubber Membrane Switch
How to clean silicone rubber? To clean the silicone rubber membrane switch, use a mild detergent and a soft cloth. First, turn off the power and remove the keycaps. Use a slightly damp soft cloth to gently wipe the switch and surrounding areas to remove dust and stains. If the stains are stubborn, wipe with ...
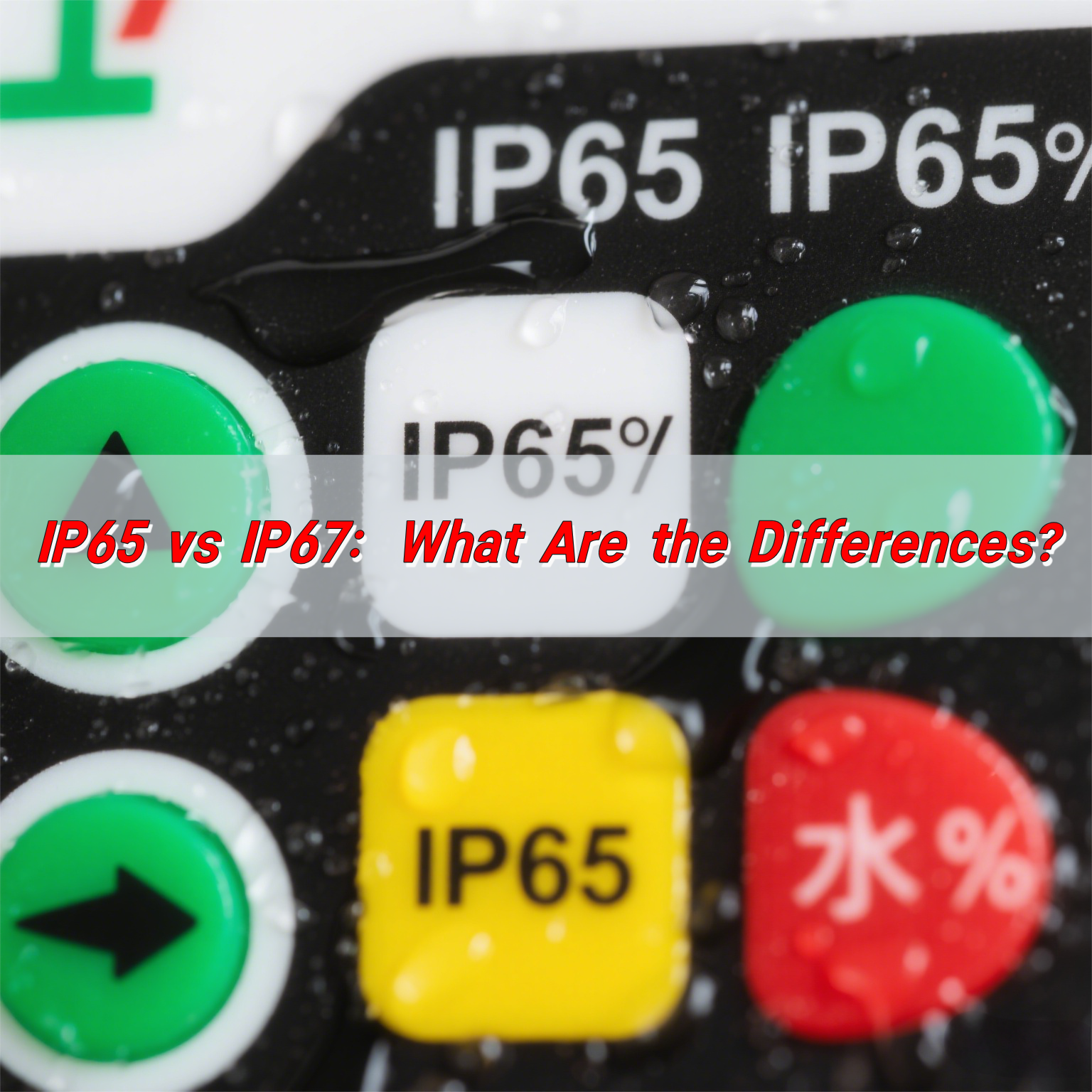
IP65 vs IP67: What Are the Differences?
IP65 vs IP67? The IP65 protection level provides complete dust protection for the device and can withstand low-pressure water jets from all directions, making it suitable for ordinary outdoor environments. Based on this, IP67 allows the device to be immersed in 1 meter of water for a short period of time (usually 30 minutes) without ...
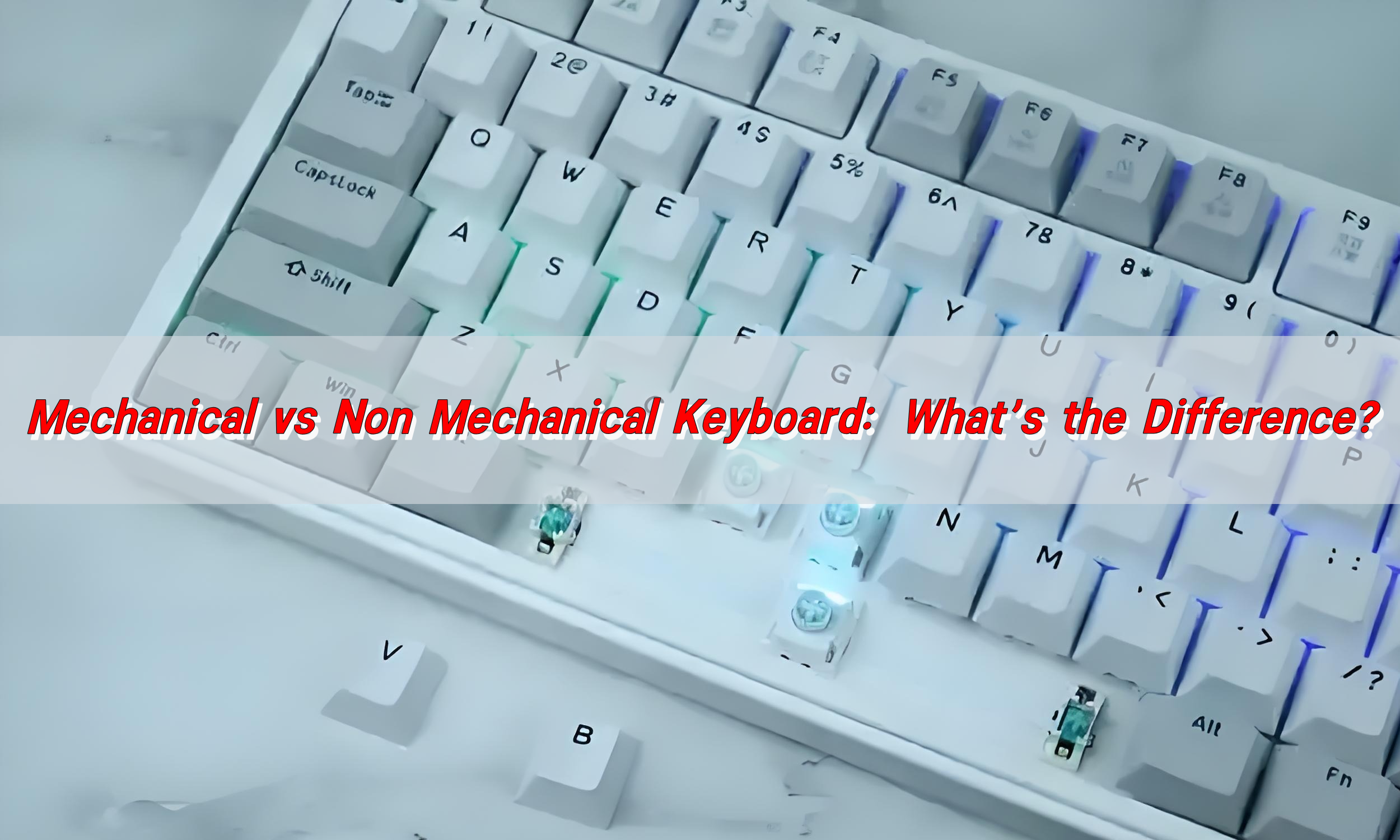
Mechanical vs Non Mechanical Keyboard: What’s the Difference?
The main differences between mechanical keyboards and non-mechanical keyboards (such as membrane keyboards) are structure, feel, durability and sound. Each key of a mechanical keyboard has an independent switch, providing a clear feel and tactile feedback, strong durability, louder sound, and is suitable for gamers. Non-mechanical keyboard keys contact the circuit board through a rubber ...
Contact us online