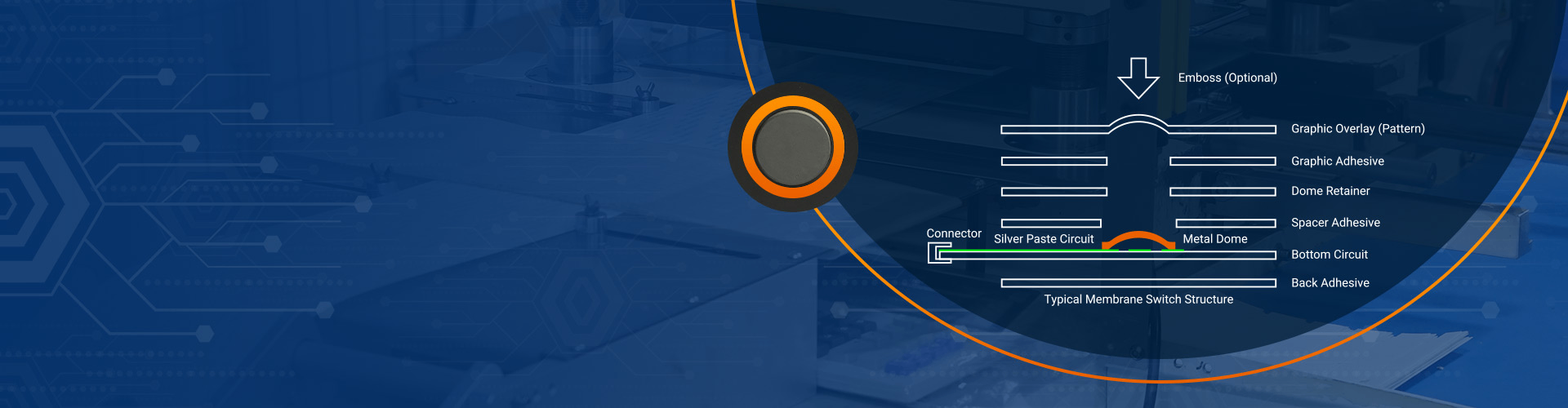
Do you understand the membrane switch manufacturing process?
Do you understand the membrane switch manufacturing process?
The membrane switch is a control system that integrates key functions, indicating components, and instrument panels. It is beautiful, lightweight, has excellent conductive properties, and has the characteristics of waterproof, dustproof, and anti-static interference. It is widely used in electronic communications, medical equipment, industrial control, Instrumentation, automotive industry, smart home and other fields. The following is a brief introduction to the membrane switch production process.
Membrane switch digital printing technology
In the previous printing of membrane switch panels, most of them were done by silk screen printing. Compared with current digital printing, silk screen printing technology is more complicated, the panel style is ordinary, and it lacks technical design style. The current digital printing technology can well display the content you want to express on the panel, and you can design specific patterns and company logos according to your needs. Just adjust the required ink to change the color and brightness in the membrane switch. Accurate expression of hue.
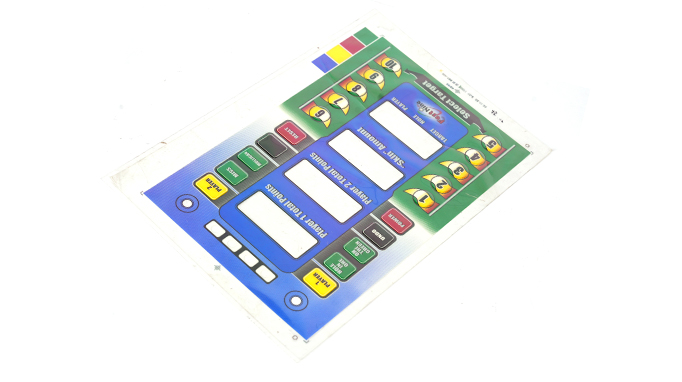
Membrane switch assembly
The main thing is to drill holes for the buttons on the membrane switch and determine the hole positions. First determine the hole positions according to the drawings, and then design a specific mold for mass production. When producing molds, make sure there are no skews or inaccurate positions.
The key position in the membrane switch is usually assembled with a metal dome. When the product has high requirements for the stability of the resistance and key sensitivity, a gold-plated dome can be used. Before assembling the dome, you need to place the dome on the PET film in a good position. Use tweezers to pick up the dome and place it at the key position on the circuit to ensure that the position is centered and will not affect the later use of the membrane switch.
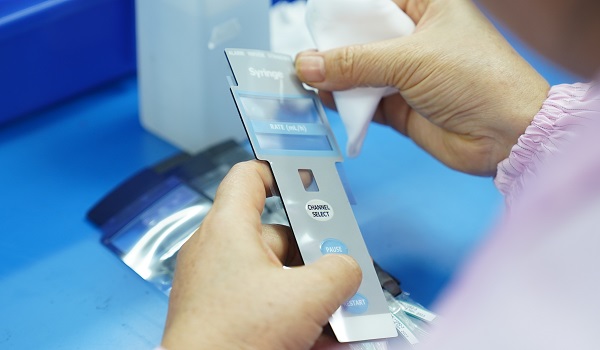
According to customer needs, we can also provide circuit board production and assembly, combine the PCB with the metal dome, and assemble the energized membrane switch panel. The film layer between the metal dome array and the PCB is connected through 3M glue, which has good sealing and adsorption effects. Prevent bacteria from entering the membrane switch during use and affecting the product life.
Membrane switch detection
First, inspect the appearance to see if there are obvious dry defects on the outside. The main purpose is to check whether the pattern on the membrane switch panel is misprinted, deinked, or scratched, and whether the button bump position is offset.
The second step is functional testing, which requires a 100% full inspection of the function of the membrane switch, and no open circuit, short circuit, poor insulation, etc.; products with LED lights must not have leakage. At the same time, check whether the resistance value of the membrane switch button is in compliance with the regulations and whether the current is stable.
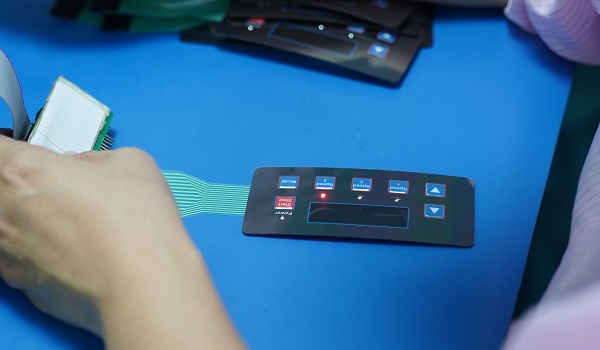
Finally, there is performance testing. Life span testing is the main concern of customers. The metal dome produced by Best Technology has been measured to be able to reach 5 million normal presses and still has a rebound effect. However, the life span test needs to be based on the conditions such as no deformation or damage on the surface of the membrane switch, and no damage to the structural layer. However, in actual applications, there will be a span of time and the impact of environmental changes on the product. Most life tests are measured under ideal conditions.
Based on the above introduction, I believe you have already understood our membrane switch panels. If your products have applications for membrane switch products, you are welcome to inquire and we will provide professional answers and help to your needs.
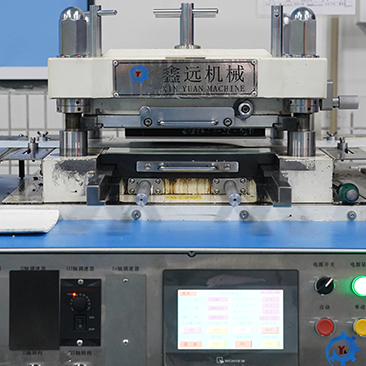
What is a Custom Capacitive Switch? A custom capacitive switch senses touch through capacitance changes. When you touch a capacitive switch, the electricity stored in your body interacts with conductive material in the switch. The switch senses the resulting change in capacitance and reacts according to its programming. Capacitive touch technologies are becoming increasingly popular, and ...
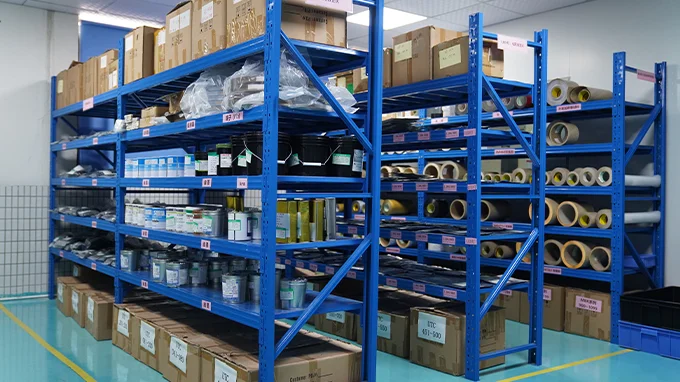
We know, quality is the core of a product, so we always proceed many inspections and measurement of membrane switch to make sure the high quality and reliability. Below are some generally methods and inspect items in Yu An electronics, from this you can know how we guarantee the quality of the membrane keypads. 1. Shape ...
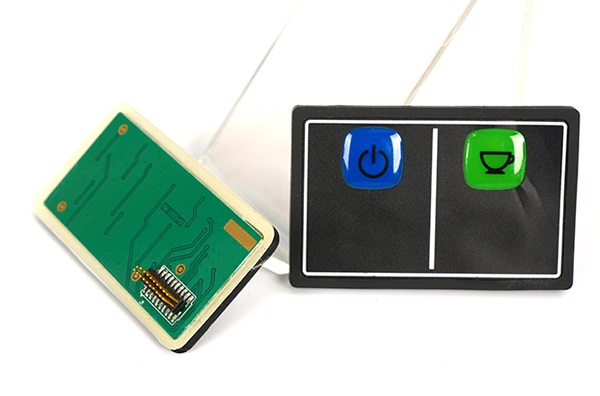
Membrane switch is a thin PET sheet with contacts, often be used as a switch in PCB, FPC and other circuit boards, and plays an important role in the touch switch between the user and the control device. The contact on the film key is located on the conductive part of the PCB board (mostly ...
Tags:
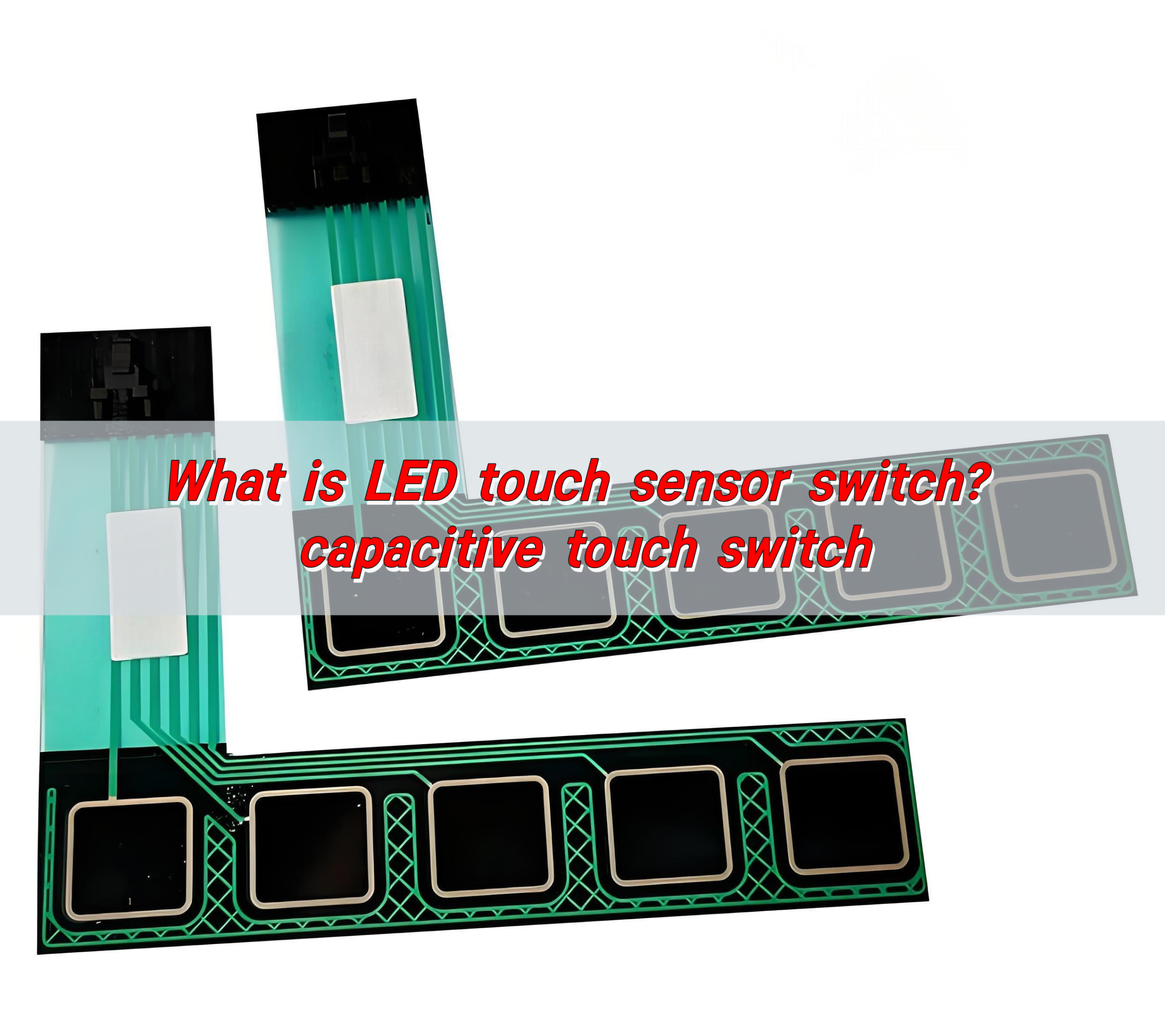
What is LED touch sensor switch? capacitive touch switch
The LED touch sensor switch is an electronic component that combines an LED light and a touch sensor. It controls the on and off of the LED light by touching it, achieving energy-saving and convenient lighting control. It uses capacitive sensing technology to detect human proximity or touch, thereby controlling the on and off of ...
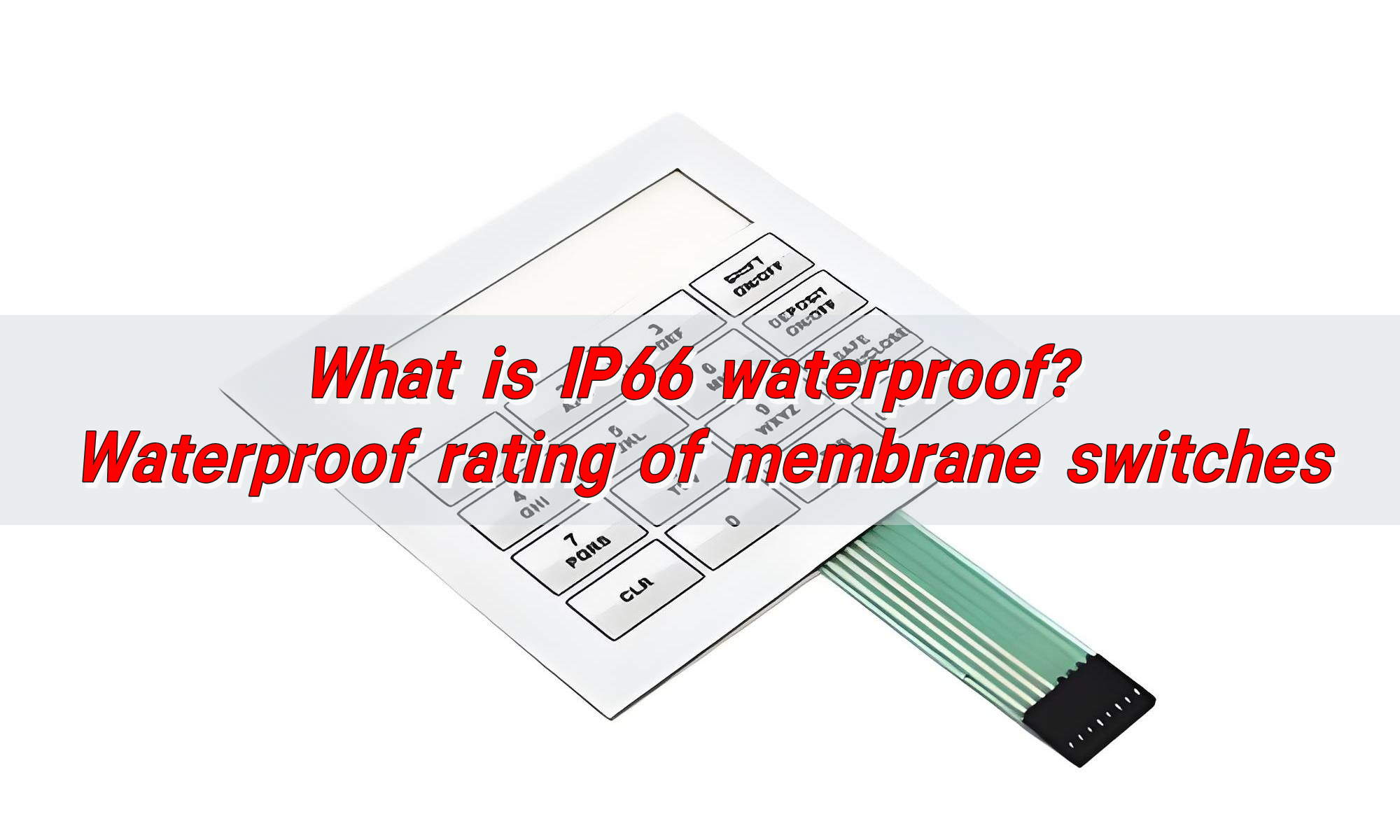
What is IP66 Waterproof? Waterproof Rating of Membrane Switches
The IP66 waterproof rating means that the device is completely protected from dust ingress and can withstand strong water jets. The waterproof rating of membrane switches can usually reach IP67, which is achieved through special processes and materials to ensure its reliability in humid or rainy environments. This performance makes membrane switches suitable for scenes ...
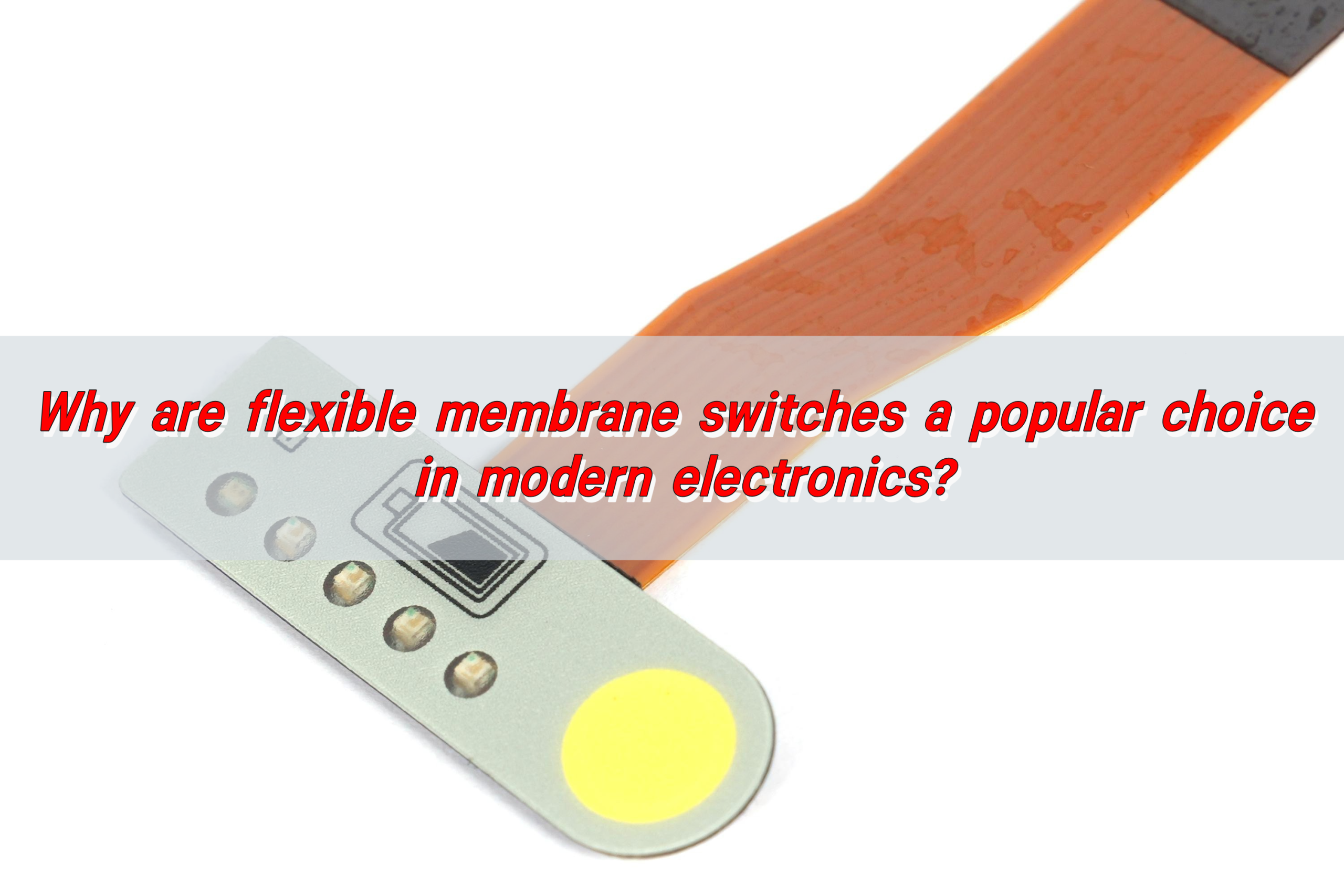
Why are flexible membrane switches a popular choice in modern electronics?
Flexible membrane switches are popular in modern electronic products due to their flexibility, thinness and economy. They not only adapt to complex curved surfaces and achieve flexible design, but also have environmental adaptability such as waterproof and dustproof. In addition, they support multi-function integration, such as LED indicators and sound feedback, to enhance user experience. ...
Contact us online